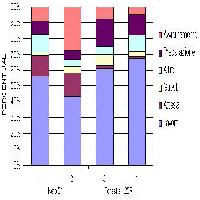
Productivity and costs of fully mechanized harvesting in Italian Appenines’ chestnut coppices
Forest@ - Journal of Silviculture and Forest Ecology, Volume 4, Pages 51-59 (2007)
doi: https://doi.org/10.3832/efor0437-0040051
Published: Mar 21, 2007 - Copyright © 2007 SISEF
Research Articles
Abstract
The paper deals with the role of mechanization in the treatment of chestnut coppice forests in the Italian Apennines. Two harvesting companies operating with mechanical processor in four different contexts in Liguria and in Tuscany regions were analyzed. The first enterprise was using a Keto 51 head mounted on a Valmet farm tractor, whereas the second one a Foresteri 25RH installed on a 14 tonne Caterpillar tracked excavator. Field data collection allowed detailing the operational methods applied by these enterprises and provided interesting figures: the rate of utilization of both processors was about 64%, and their productivity varied between 7 and 10 m3/net hour. Daily productivity was found in the range of 25-40 m3 using Keto 51, and 40-55 m3 for the Foresteri 25RH. Machine operating cost (including labour) was rated at about 100 €/scheduled hour. Considering the financial incentives provided by the regional Rural Development Programme, harvesting costs have been estimated in the range of 15 and 33 €/m3, allowing the two companies to carry out profitable activities in the local markets.
Keywords
Forest mechanisation, Operating costs, Apennines, Mechanical processors, Castanea sativa
Introduzione
Le imprese boschive che operano nelle regioni centrali sono spesso associate all’ipotesi di condizioni organizzative arretrate e in particolare all’impiego di metodi di utilizzazione obsoleti. Negli ultimi anni il divario tecnologico tra mezzi e metodi applicati nell’arco appenninico ed in quello alpino si è invece fortemente ridotto, grazie non soltanto al desiderio delle singole imprese nel mantenersi in posizione competitiva sui mercati locali, ma anche alle recenti iniziative di incentivazione legate alle politiche di sviluppo rurale ([6]). In particolare la misura I dei Piani di Sviluppo Rurale (PSR) 2000-2006 ha dato la possibilità a molte ditte boschive di modernizzare il proprio parco macchine aumentando la sicurezza e la produttività dei cantieri. L’acquisizione di nuovi mezzi ha messo le imprese in condizione di poter intervenire anche in quelle zone della dorsale appenninica dove la carenza di strade ed infrastrutture utili al passaggio dei mezzi e l’accidentalità del terreno abbassano fortemente il margine di redditività delle operazioni di utilizzazione.
Il presente studio cerca di inquadrare il ruolo della meccanizzazione nell’abbattimento e allestimento dei boschi cedui di castagno sull’Appennino ligure e toscano. In particolare, si è voluto documentare e valutare la potenzialità d’uso dei combinati[1] (processore più motrice) nelle paline e nei popolamenti abbandonati o da poco ripristinati alla gestione ordinaria.
In Italia, le prime sperimentazioni sull’utilizzo di processori su castagno risalgono alla fine degli anni 90 ([8]), subito dopo il boom commerciale del ’99, favorito dall’uragano Lothar che colpì il centro Europa, e in particolare la Francia, con l’abbattimento di 193 milioni di metri cubi di legname da esboscare in tempi brevi. Da allora queste macchine si sono progressivamente diffuse anche nelle regioni appenniniche centro-occidentali, dove vi è un’alta concentrazione di popolamenti a ceduo, spesso abbandonati. La forte versatilità di queste macchine, pensata proprio per facilitare il lavoro e per colmare le carenze di mano d’opera, ha un ruolo determinante per conciliare le esigenze del mercato locale e quelle aziendali.
Per monitorare gli spazi di innovazione nell’utilizzo dei combinati, gli Autori hanno seguito le attività boschive di due ditte che utilizzano il processore soprattutto per la lavorazione in bosco del legname di castagno ad uso di paleria agricola, da bioingegneria e tondelli di semilavorato destinato alla produzione di mobili rustici. Il rinnovamento dei mezzi ha permesso alle due ditte di allargare il proprio giro d’affari e nel contempo di specializzarsi nella lavorazione del castagno; entrambe sono riuscite a soddisfare un maggior numero di commesse, grazie all’aumento della produttività e al miglioramento qualitativo dei propri prodotti.
Materiali e metodi
Le macchine
Le macchine esaminate sono due combinati leggeri concepiti per lavorare legname di piccole e medie dimensioni. Un’impresa (impresa “A”) ha optato per l’acquisto di un processore Keto 51 montato su trattore Valmet 8060, impiegato in abbinamento con una gru a cavo. La scelta di un trattore agricolo come motrice ha permesso all’impresa di utilizzare più intensamente la macchina che, con l’ausilio di un rimorchio, è stata impiegata anche per il trasporto del legname al rientro giornaliero in deposito. Inoltre, il montaggio su trattore ha reso più agevole lo spostamento tra i siti di lavoro, evitando costi supplementari dovuti al trasporto su carrellone. L’altra impresa (impresa “B”), al contrario, ha scelto di acquistare un escavatore cingolato CAT 312CL e di abbinarlo al processore Foresteri 25RH, allo scopo di potersi muovere liberamente all’interno del popolamento ed effettuare l’abbattimento e l’allestimento direttamente sul letto di caduta delle piante. La compattezza, la resistenza e l’agilità dell’escavatore cingolato lo rendono particolarmente adatto a muoversi in ambienti con pendenze relativamente basse, ma di difficile accessibilità, per la presenza di rocce affioranti. La scelta di acquistare un cingolato è stata basata anche sull’ampiezza della zona operativa dell’azienda che, lavorando su appezzamenti spesso accorpati e vicino alla propria sede, non necessita di spostamenti su lunghe distanze della macchina. Il Foresteri 25RH è un processore molto compatto che impiega rulli di alimentazione con elementi di aderenza appositamente modificati dal concessionario per la lavorazione del castagno.
Entrambi i combinati sono stati acquistati nuovi nel 2002 e le rispettive ditte hanno usufruito della sovvenzione del 40% messa a disposizione dalle Regioni in base al PSR 2000-2006. Le due unità (processore / motrice) sono state acquistate con un costo di investimento di circa 130.000 € ciascuna, e vengono in media impiegate per 800 ore lavorative l’anno. Le motrici hanno grande flessibilità di impiego e possono essere usate anche in altri ambiti lavorativi o per svolgere piccoli compiti accessori; questo le rende facilmente ricollocabili sul mercato dell’usato, qualora le due imprese decidessero di ammodernare il parco macchine. La Tab. 1 riporta le caratteristiche tecniche dei due combinati.
Tab. 1 - Caratteristiche dei due combinati.
Processore | Impresa “A” | Impresa “B” |
---|---|---|
Modello | Keto 51 | Foresteri 25RH |
Marca | Nokka | Foresteri |
Ø max. di taglio (cm) | 37 | 67 |
Ø max. di sramatura (cm) | 32 | 55 |
N° coltelli | 1 fisso | 1 fisso |
+3 mobili | + 4 mobili | |
Sistema di alimentazione | cingoli | rulli |
Velocità alimentazione (m/s) | 4 | 3.8 |
Forza di alimentazione (kN) | 15 | 23 |
Lunghezza barra (cm) | 54 | - |
Passo catena (pcs) | 0.404 | 0.404 |
Peso (kg) | 460 | 770 |
Pressione idraulica min. (Bar) | 210 | 210-230 |
Portata idraulica min (l/min) | 160 | 190-210 |
Altezza | 1300 | - |
Larghezza coltelli aperti/chiusi (mm) | 1010/850 | - |
Lunghezza (mm) | 1100 | - |
Potenza base di funzionamento (Kw) | 60 | 75-90 |
Motrice | Impresa “A” | Impresa “B” |
Tipo | Trattore | Escavatore |
Marca | Valmet 8060 | CAT 312CL |
Potenza (cv) | 110 | 100 |
Peso (kg) | 8000 | 13 |
Trasmissione | idraulico-meccanica | Idraulico-meccanica |
Velocità max. (km/h) | 40 | - |
Sbraccio (m) | 7.5 | 7.5 |
Alzata a sbraccio max (kg) | 650 | - |
Rotazione (gradi) | - | 360 |
Larghezza (mm) | 2250 | 2200 |
Le prove
I processori sono stati osservati durante il periodo invernale (2004-2005) su quattro cantieri di ceduo di castagno con caratteristiche differenti. Al fine di evitare che condizioni operative particolari potessero influenzare la raccolta dei dati, i periodi di rilievo sono stati ripetuti e casuali. Le prime due tagliate erano situate in Alta Val Bormida, nelle località di Calizzano e di Millesimo, dove le prove sono state effettuate nel periodo compreso tra il 4 novembre ed il 18 febbraio. Gli altri due cantieri erano localizzati sul Monte Amiata, in località di Abbadia di S.Salvatore ed i rilievi sono stati eseguiti tra il 10 gennaio ed il 1 aprile. La Tab. 2 riporta le caratteristiche principali delle quattro zone, che possono considerarsi rappresentative della odierna struttura dei popolamenti di castagno sul territorio nazionale.
Tab. 2 - Descrizione stazionale dei siti dei rilievi.
Caratteristiche | 1 | 2 | 3 | 4 |
---|---|---|---|---|
Località | Calizzano (SV) | Millesimo (SV) | Abbadia S. Salvatore (SI) |
Abbadia S. Salvatore (SI) |
Quota (m. s.l.m.) | 850-930 | 825-900 | 1058 | 850 |
Esposizione | Nord | Sud-Est | Sud-Est | Sud-Est |
Condizione suolo | Bagnato | Ghiacciato | Bagnato | Bagnato |
Tipo roccia madre | Metamorfica | Metamorfica | Magmatica | Magmatica |
Tagliata totale (ha) | 1.3 | 1.5 | 8 | 2 |
Area studio (ha) | 0.6 | 0.6 | 0.8 | 0.9 |
Pendenza (%) | 40-60 | 10-50 | 10-40 | 10-15 |
Distanza cantiere/deposito (km) | 6 strada, 3 st. trattorabile |
11 strada, 3 st. trattorabile |
2.5 strada, 2.5 st. trattorabile |
2 strada, 1.3 st. trattorabile |
Accidentalità | Forte | Forte | Moderata | Bassa |
Specie presenti | Castagno 90%, Faggio 10% |
Castagno 100% | Castagno 100% | Castagno 100% |
Età (anni) | 50 | 18 | 24 | 26 |
Altezza media (m) | - | 12-15 | 15-20 | 15-20 |
Diametro medio (cm) | 18 | 14 | 14 | 17 |
Ceppaie (n/ha) | 840 | 800 | 740 | 500 |
Polloni commerciabili (> 5 cm - n/ha) |
1400 | 2150 | 1990 | 850 |
Polloni morti (n/ha) | 880 | 1000 | 650 | 25 |
Altre specie (n/ha) | 300 | - | - | - |
Matricine (n/ha) | n.r. | 100 | 65 | 75 |
Media polloni/ceppaia (n) | 2 | 4 | 3-4 | 2 |
Volume (m3/ha) | 230 | 165 | 200 | 188 |
In particolare, nei cantieri 1 e 2, le ceduazioni hanno avuto lo scopo principale di rinvigorire le ceppaie di castagno e di ristabilire un trattamento a ceduo per la produzione di pali. La tagliata 1 era caratterizzata da un popolamento invecchiato di circa cinquanta anni con la presenza di individui di grande dimensione e forte ramosità, mentre il secondo cantiere era la rimanenza di un vecchio taglio non completato, disposto su due appezzamenti di piccola dimensione e costituito da un giovane popolamento con individui slanciati e sottili. Entrambi gli appezzamenti erano di difficile accessibilità, sia per le distanze da percorrere, che per la cattiva qualità delle strade utilizzabili e per i limitatissimi spazi per la lavorazione.
In generale, in questi cantieri è stata impiegata una gru a cavo per l’esbosco delle piante intere, un processore generalmente posizionato sotto la teleferica ed un trattore dotato di gru idraulica per il carico degli assortimenti su due rimorchi. Il processore aveva il compito di prelevare la pianta dal letto di accumulo, allestirla, sezionarla ed accatastare separatamente i due assortimenti prodotti: pali o legname da triturazione. Nella lavorazione di piante la cui ramificazione era particolarmente densa od il tronco risultava troppo sinuoso, il processore ha lavorato con i coltelli semi-aperti per evitare che si piantassero nel legno: qui la sramatura è stata effettuata con la rottura dei rami attraverso la forza esercitata dalla chiusura dei coltelli, più che con un taglio pulito. Di fronte a piante biforcate o con grosse branche, il processore operava sezionando la pianta nel punto di biforcazione e lavorando in seguito i singoli rami. Le piante di dimensioni troppo elevate per essere trattate con il processore sono state separate e accatastate a bordo strada per essere allestite con la motosega in un secondo momento. Al contrario, in presenza di individui di piccole dimensioni, il processore ha lavorato più piante contemporaneamente. Alla fine della sramatura e depezzatura della pianta il processore depositava a bordo piazzola il cimale per poi ricominciare le operazioni su un altro individuo. Il piazzale di lavorazione veniva sgomberato velocemente dal trattore dotato di caricatore idraulico, che posizionava il legname lavorato sul rimorchio e accatastava le ramaglie, formando mucchi molto voluminosi.
Le ceduazioni nelle prove 3 e 4 sono consistite in tagli di fine turno, su cedui regolarmente gestiti per la produzione primaria di pali, e secondariamente di toppi da sega e travame. Gli scarti invece sono stati destinati alla vicina fabbrica di pannelli di Radicofani. Entrambi i popolamenti si presentavano con ceppaie ben sviluppate, allargate e con individui dritti, slanciati, con chioma fine e alta.
Nei cantieri della impresa “B” si è sempre utilizzato il combinato in bosco, procedendo lungo le linee di massima pendenza e lavorando per corridoi, quasi mai lineari e paralleli, a causa della particolare morfologia del territorio. Con il Foresteri 25RH si è effettuata agevolmente la lavorazione diretta dei polloni, riuscendo ad accedere facilmente a ciascuna singola pianta senza arrecare danno alle ceppaie o agli altri individui. L’allestimento della pianta è stato realizzato direttamente nel raggio d’azione della macchina, che nel cantiere n° 4 ha effettuato anche l’abbattimento. La pianta era allestita sul posto creando mucchi di assortimenti misti. Le ramaglie invece erano raggruppate e posizionate lungo i corridoi di lavorazione del processore. Un secondo escavatore munito di gru idraulica aveva il compito di spostare il legname, successivamente diviso per assortimenti da un operaio. Lo sgombero del materiale è stato eseguito tramite trattore con rimorchio o con autocarro, se il sito ne consentiva l’accesso. Alla fine del lavoro due operai sono passati ad abbassare le ceppaie e ripulire il cantiere.
Il terzo cantiere insisteva su un versante a forte pendenza e pertanto si è proceduto al taglio manuale delle piante, impiegando due operatori per una mezza giornata. Le piante abbattute sono state concentrate a bordo strada con il secondo escavatore, e quindi facilmente lavorate dal processore, che ha prodotto cumuli di assortimenti in breve tempo.
Rilievi
Il rilievo consisteva in uno studio classico dei tempi di lavoro. Ogni giornata lavorativa è stata suddivisa in varie operazioni, e queste a loro volta in fasi operative, rilevate secondo la metodologia di secondo livello suggerita nel documento “Rilievo in successione dei tempi delle fasi di lavoro” ([1]). Contemporaneamente alla misurazione dei tempi di lavoro, si sono rilevati i quantitativi di legname lavorati: nel cantiere 1 questi sono stati misurati contando tutti i pezzi dei vari assortimenti prodotti, e quindi cubando manualmente tutti i pali e una campionatura giornaliera del materiale da triturazione. Nei cantieri 2, 3 e 4 i dati circa le piante lavorate, gli assortimenti prodotti e i relativi volumi sono stati direttamente elaborati dal computer di bordo della macchina. Anche qui sono stati effettuati opportuni campionamenti, per confermare l’attendibilità dei dati forniti dal computer. Anche per questi cantieri, si è potuto risalire alla densità media del materiale lavorato attraverso la pesata dei carichi prodotti. La Tab. 3 riporta in sintesi la produzione totale dei quattro cantieri.
Tab. 3 - Produzione ottenuta dai quattro interventi (dati relativi all’intera superficie dell’area di studio).
Produzione | 1 | 2 | 3 | 4 | ||||
---|---|---|---|---|---|---|---|---|
m3 | Pezzi | m3 | Pezzi | m3 | Pezzi | m3 | Pezzi | |
Pali | 54.57 | 502 | 29.53 | 834 | 110.54 | 7732 | 105.24 | 4506 |
Triturazione | 83.39 | 2958 | 69.06 | 4625 | 17.65 | - | 15.37 | - |
Travame | - | - | - | - | 34.32 | 1094 | 48.46 | 1157 |
Legname da sega | 6.1 | 12 | 0 | 0 | 0 | 0 | 0 | 0 |
Totale | 144.06 | 3472 | 98.53 | 5450 | 162.54 | 8838 | 169.07 | 5663 |
Tot. Piante | 772 | 1349 | 1637 | 916 | ||||
N. pezzi medi per pianta | 4.5 | 4 | 5.4 | 6 | ||||
Volume medio unitario pianta | 0.18 | 0.07 | 0.09 | 0.16 | ||||
Peso totale (t) | 152.8 | 98 | 146.8 | 152.7 |
Risultati e discussione
La lavorazione delle tagliate 1 e 2 ha permesso di ottenere nella maggior parte materiale da triturazione, evidenziando la scarsa qualità dei popolamenti trattati e la necessità di utilizzare la macchina nel pieno delle sue potenzialità per produrre quantità sufficientemente remunerative. Nelle altre due tagliate invece la qualità del prodotto era migliore, e ciò ha permesso un utilizzo del processore meno intenso, finalizzato ad allestire materiale di qualità superiore.
I principali risultati dello studio sui tempi di lavoro sono riportati in Tab. 4 e nella Fig. 1. Il processore Keto 51 montato su trattore Valmet 8060 ha lavorato in cantiere per più del 60% del tempo ed ha subito un tempo di attesa sotto la teleferica compreso tra 15 e 22%. Nel primo cantiere, l’esbosco di piante troppo grosse per essere allestite con il processore ha determinato una quota importante di altri tempi di lavoro (“Altro”: 13%), dovuta all’accatastamento separato di queste piante e alla loro lavorazione manuale con motosega.
Tab. 4 - Tempi di lavoro (in secondi sessagesimali) e produttività riscontrate nei quattro cantieri di prova. (1) calcolato in base al tempo produttivo del combinato diviso per il tempo di osservazione in %; (2) calcolata in base alla durata di tutte le operazioni giornaliere (T/Volume totale prodotto); (3) calcolata in base ai tempi netti effettivi di abbattimento ed allestimento (TNE/Volume totale prodotto); (4) si riferisce alle giornate effettivamente passate in cantiere.
Operazioni | Cantiere 1 | Cantiere 2 | Cantiere 3 | Cantiere 4 |
---|---|---|---|---|
(Keto) | (Keto) | (Foresteri) | (Foresteri) | |
Lavoro | 64219 | 53406 | 72863 | 62886 |
Attesa | 14492 | 18462 | 2058 | 713 |
Guasti | 2331 | 5095 | 8330 | 2971 |
Altro | 12946 | 5400 | 6263 | 9571 |
Totale lavoro cantiere (TL) | 93988 | 82363 | 89514 | 76141 |
Preparazione | 9470 | 7102 | 20731 | 12246 |
Avvicinamento al cantiere | 10082 | 33611 | 8749 | 4392 |
Totale tempo osservazione (T) | 113540 | 123076 | 118994 | 92779 |
Totale ore (T) | 31.53 | 34.19 | 33.05 | 25.77 |
Totale giornate di osservazione (4) | 5 | 4 | 6 | 5 |
Tasso d’utilizzazione (1) (%) | 60 | 69 | 61 | 67 |
Produttività lorda (2) (m 3 /ora) | 5 | 3 | 5 | 7 |
Produttività netta (3) (m 3 /ora) | 9 | 7 | 8 | 10 |
Nel secondo cantiere, la grande distanza dell’imposto dal deposito ha ridotto molto la quota di lavoro effettivo, perché il trasferimento al luogo di lavoro comportava un notevole dispendio di tempo. Probabilmente, lasciando il combinato in cantiere e spostandosi con un fuoristrada - come facevano gli operatori della teleferica - si sarebbero ridotti i tempi di trasferimento, aumentando la quota di tempo a disposizione per il lavoro. Nelle due prove liguri la fase organizzativa dei cantieri ha subito delle continue modificazioni, dovute alle particolari caratteristiche del popolamento che rendevano difficoltosa tutta la fase di utilizzazione. Nonostante le difficoltà dei cantieri esaminati e le conseguenti problematiche gestionali, i tempi del Keto 51 risultano paragonabili a quelli verificati in altri ambienti di tipo alpino dove tali sistemi sono già da tempo applicati in popolamenti di conifere.
L’impresa “B” ha lavorato con la macchina all’interno del lotto; con questo sistema le varie operazioni si susseguono l’una all’altra, evitando interferenze dovute dalla presenza di altri operatori o macchine che devono coordinarsi con il processore. In effetti, come evidenziato nella Fig. 1, le principali voci di tempo improduttivo sono i guasti e la preparazione, e non le interferenze tra le diverse operazioni. La preparazione al lavoro occupa circa 50 minuti giornalieri, e risulta molto importante dal momento che la macchina funziona sempre ad alti regimi ed ha la necessità di essere controllata e riscaldata prima di cominciare a lavorare. Sia i guasti che le operazioni di preparazione risultano occupare complessivamente dal 16% al 24% del tempo totale di permanenza in cantiere.
In funzione delle dimensioni della pianta trattata, compresa tra 0.07 e 0.18 m3, il Keto 51 ha mantenuto una produttività oraria netta compresa tra i 7 e 9 m3 /ora, mentre il Foresteri 25RH tra gli 8 ed i 10 m3/ora netta. Le due macchine, pur essendo utilizzate secondo due schemi organizzativi molto differenti, hanno entrambe evidenziato un coefficiente medio di utilizzazione[2] pari a 64%. Il tempo produttivo[3] considerato per il combinato Foresteri 25RH/CAT312CL è stata la sola fase del lavoro, perché impiegato esclusivamente per abbattere ed allestire le piante, mentre per il combinato Keto 51/Valmet8060 è stata considerata la fase di lavoro, in cui si effettua il solo allestimento, ed il tempo di avvicinamento, poiché il viaggio con carico ed il viaggio a vuoto dal bosco fanno parte della fase produttiva dell’operazione di esbosco e trasporto del materiale in cui la macchina viene normalmente impiegata.
Utilizzando i dati forniti dagli operatori dei due mezzi e dai proprietari delle due rispettive imprese si è proceduto al calcolo dei costi-macchina (Tab. 5), in base alla metodologia di Miyata ([5]). I costi sono stati stimati pari a 115 €/ora per il combinato Keto/Valmet e 118 €/ora per il Foresteri/Caterpillar. Questi valori possono essere considerati indicativi del range di costi per mezzi con le medesime caratteristiche tecniche, operative e commerciali.
Tab. 5 - Calcolo del costo di esercizio delle due attrezzature, con e senza incentivo all’acquisto.
Dati Tecnici | Simbolo | Formule | Costo Keto 51 |
Costo con incentivi (40%) |
Costo Foresteri 25 |
Costo con incentivi (40%) |
---|---|---|---|---|---|---|
Prezzo d’acquisto | P | - | 132000 | 79200 | 130000 | 78000 |
Valore di recupero | S | 10% P | 13200 | 13200 | 13000 | 13000 |
Durata tecnica (anni) | n | - | 7 | 7 | 7 | 7 |
Potenza processore | hp | - | 110 | 110 | 100 | 100 |
Potenza processore (kw) | Pt | Hp*0.736 | 81 | 81 | 74 | 74 |
Ore lavoro annuali | SHY | - | 800 | 800 | 760 | 760 |
Investimento medio annuo | AI | ((P-S)*(n+1))/ (2*n))+S |
81086 | 50914 | 79857 | 50143 |
Coefficiente di manutenzione | RMr | % Depr | 75 | 75 | 75 | 75 |
Tasso d’interesse | r | % | 6 | 6 | 6 | 6 |
Coeff. tasse, assicurazione e rimessaggio | ITGr | % | 12 | 12 | 12 | 12 |
Consumo combustibile (l/h) | Fc | (0.21*Pt*Putil1) | 12.5 | 12.5 | 13 | 13 |
Consumo lubrificante (l/h) | Lc | (0.006*Pt*Putil) | 0.365 | 0.365 | 0.377 | 0.377 |
Prezzo combustibile | Fp | - | 1.1 | 1.1 | 1.1 | 1.1 |
Prezzo lubrificante | Lp | %Fp | 35 | 35 | 35 | 35 |
Costo mano d’opera lordo | WB | - | 18 | 18 | 18 | 18 |
COSTI FISSI | ||||||
Ammortamento | Depr | (P-S)/n | 16971 | 9429 | 16714 | 9286 |
Interessi | IN | AI*r | 4865 | 3055 | 4791 | 3009 |
Tasse, assicurazione, garage | ITG | AI*ITGr | 9730 | 9730 | 9583 | 9583 |
Costi fissi per ora lorda | OC | Depr+IN+ITG/SHY | 39.46 | 27.77 | 40.91 | 28.79 |
COSTI VARIABILI | ||||||
Riparazione e manutenzione | RM | (Depr*RMr)/SHY | 15.91 | 15.91 | 16.49 | 16.49 |
Combustibile | FC | (Fc*Fp)/DSH | 13.75 | 13.75 | 14.30 | 14.30 |
Lubrificante | LC | (Lc*Lp)/DSH | 4.81 | 4.81 | 5.01 | 5.01 |
Manodopera | WB | WB | 18 | 18 | 18 | 18 |
Costi variabili per ora lorda | Opc | RM+FC+LC+WB | 52.47 | 52.47 | 53.8 | 53.8 |
Costo operativo tot. | OT | OC+Opc | 92 | 80 | 95 | 83 |
Spese generali e utile d’impresa | SGU | 25%OT | 23 | 20.1 | 23.7 | 20.6 |
COSTO TOTALE | CT | OT+SGU | 115 | 100 | 118 | 103 |
In particolare, il computo del costo di esercizio è stato basato sulle seguenti assunzioni: un valore di recupero (S) del 10%; una durata tecnica (n) di 7 anni, coerente con l’ipotesi di un monte-ore produttivo (PH) relativamente basso; un coefficiente di manutenzione (RMr) del 75%, intermedio tra quello utilizzato per i mezzi agricoli (50%) e quello normalmente proposto (100%) da Myata. Il costo orario della manodopera è stato valutato pari a 18 €, con riferimento al costo relativo all’impiego di un operaio specializzato. Infine, per calcolare l’effettivo consumo del combustibile e del lubrificante è stato moltiplicato al consumo specifico medio dei motori diesel un coefficiente (Putil) che consideri l’effettivo regime di funzionamento del motore delle due macchine: del 0.75 per il Keto 51, e del 0.85 per l’escavatore, tenendo conto che quest’ultimo lavora in modo più continuativo, e quasi sempre al limite della sua potenzialità. La quota relativa ai consumi risulta comunque combaciare con quella dichiarata dai conduttori delle due vetture (circa 100 l/gg. di gasolio).
L’utilizzo, da parte delle due imprese, dell’incentivo del 40% sul valore dell’acquisto del combinato, messo a disposizione dal PSR 2000-2006, ha permesso di ridurre il costo macchina a 100 €/ora per il Keto 51 e a 103 €/ora per il Foresteri 25RH. Per la stima dei costi con incentivo il valore di recupero (S), le spese di riparazione e manutenzione (RM) e quelle per tasse, assicurazione e rimessaggio (ITG), non rientrando nelle condizioni di incentivazione ed essendo calcolate come percentuale di un costo a nuovo della macchina, sono state mantenute pari a quelle della condizione senza incentivo.
Sulla base dei risultati delle stime dei costi-macchina è stato possibile ricavare il costo di lavorazione per unità di prodotto[4] relativo ai due processori, che è risultato di 20 €/m3 e di 33 €/m3 rispettivamente per i due cantieri lavorati con il Keto 51 e di 20 €/m3 e di 15 €/m3 per quelli lavorati con il Foresteri 25RH.
Conclusioni
L’indagine è stata effettuata in due condizioni operative molto diverse, abbastanza comuni nel territorio appenninico: da un lato cedui semi-abbandonati e di difficile accesso, e dall’altro comprensori regolarmente sottoposti ad assestamento per produrre assortimenti remunerativi. In entrambi i casi i processori hanno dimostrato di adattarsi molto bene alle caratteristiche dei popolamenti di castagno e alle condizioni strutturali delle imprese boschive osservate (numero limitato di addetti, con un livello medio di qualificazione). L’analisi dei tempi di lavoro ha evidenziato un tasso di utilizzazione in linea con quelli rilevati in altri ambiti forestali e riportati nella bibliografia straniera ([4], [2], [3], [7]), e comune ad entrambe le macchine, nonostante le modalità d’impiego differenti.
Entrambi i mezzi sono stati impiegati su fusti relativamente piccoli, quindi in condizioni sfavorevoli al conseguimento di produttività elevate. Dove il processore era asservito ad una teleferica, la produttivitàè stata condizionata anche dalle inevitabili interferenze tra le operazioni e le attese. Questo spiega come, soprattutto in queste circostanze, sia necessario gestire e organizzare il lavoro in modo appropriato, al fine di evitare quei piccoli contrattempi che, cumulandosi, possono pregiudicare la buona riuscita del cantiere. Le macchine hanno comunque mantenuto una produttività lorda molto alta, variabile tra i 25 e i 40 m3/giorno per il processore Keto 51, e tra i 40 e i 55 m3/giorno per il processore Foresteri 25RH. Considerando l’incentivo, i costi-macchina sono risultati intorno ai 100 €/ora (produttività lorda), a cui corrispondono costi di lavorazione compresi tra i 20 e i 33 €/m3 per il Keto 51 e tra i 15 e i 20 €/m3 per il Foresteri 25 RH.
L’abbattimento, l’allestimento e il concentramento del legname sono stati effettuati con produttività almeno 4 volte superiori rispetto a quelle ottenibili con i sistemi manuali, dal momento che un operaio forestale nello stesso tipo di ceduo e con lo stesso tipo di assortimento da ottenere può arrivare a produrre in media 6 m3/giorno. Bisogna, inoltre, tenere conto che con l’uso di tecniche tradizionali possono insorgere più facilmente costi aggiuntivi dovuti ad interruzioni del lavoro in caso di mal tempo. Con queste macchine invece è possibile evitare, almeno in parte, i contrattempi dovuti a sfavorevoli condizioni climatiche che in questi ultimi anni sull’arco appenninico sembrano limitare fortemente i tempi di intervento nei periodi di taglio. Da notare infatti che la presenza di abbondante neve nel terzo cantiere non ha fermato i lavori, né ostacolato l’attività della macchina.
Le macchine esaminate sono risultate particolarmente efficaci sui popolamenti abbandonati, proprio perché vi é la presenza di individui grandi da cui si può ottenere anche una discreta produzione di pali di buona qualità. Inoltre, gli scarti, una volta concentranti e accatastati, sono pronti per essere eventualmente trasformati in cippato.
Per le ragioni sopra richiamate, il contributo del 40% alle spese d’acquisto delle macchine può ritenersi opportuno alla luce di valutazioni di convenienza pubblica, dal momento che consente di trasformare aree a macchiatico negativo in investimenti remunerativi, contribuendo a ridurre i problemi di abbandono gestionale e il mantenimento di importanti filiere di approvvigionamento locale di legname, con positivi effetti indotti nelle attività di lavorazione e commerciali a valle delle produzioni forestali.
References
Google Scholar
Google Scholar
Google Scholar
Google Scholar
Google Scholar
Google Scholar
Google Scholar
Google Scholar